
5S
Lean Factory
OpEx advisors are waiting for you
You are in the right place for OpEx (Operational Excellence) consultants! As KPI ACADEMY, we offer customized consulting services for businesses to optimize their operational processes and increase their level of excellence. Our expert OpEx consultants offer strategic solutions to increase the efficiency of businesses, reduce waste, reduce costs and gain competitive advantage. Working with our OpEx consultants, you can analyze your business processes, identify opportunities for improvement and target operational excellence.
We are waiting for you!
5S Steps
What is Lean Factory?
Value And 7 Wastes
5S Steps
5S is a management tool based on the principles of order and cleanliness.
5S creates an effective working environment in the workplace, increases productivity and supports occupational safety.
-
Extraction - Seiri
It is the step of removing unnecessary items and materials in the workplace. While ensuring that only necessary items are available at the workplace, unnecessary ones are eliminated. This step reduces space occupation and prevents unnecessary movements in the workplace.
-
Editing - Seiton
It is the step of organizing the things in the workplace. It is ensured that each item is stored in a specific place and in an orderly manner. This step allows materials to be easily found and used, reducing wasted time at work.
-
Cleaning - Seiso
It is the step of cleaning the workplace. Cleaning routines are established and done regularly. A clean working environment increases job security and increases employee morale and motivation.
-
Standardization - Seiketsu
It is a step to ensure the continuity of 5S applications in the workplace. Standard business practices, procedures and instructions are established. This step supports standardization in the workplace by ensuring continuity and consistency.
-
Discipline - Shitsuke
It is the step of maintaining and maintaining 5S practices in a disciplined manner. Employees are encouraged to adhere to the 5S principles and integrate these principles into their daily routines. This step contributes to the development of a culture of continuous improvement and sustainability.
Lean Factory
Lean Factory is a business approach designed to reduce waste, speed up processes and respond more quickly to customer demands. The basic principles of the Lean Factory are elimination of activities that do not create value, fluidization of processes, reduction of stock amount, fast and flexible production structure and quality-oriented work. Lean Factory enables businesses to reduce costs, increase customer satisfaction and gain competitive advantage.
Value And 7 Wastes
Value can be defined as any feature, attribute or transaction that a customer pays for a product or service that makes a difference to it. The aim of businesses is to gain competitive advantage by offering products and services that add value to the customer. However, various wastes and wastes can be found in business processes. At this point, the concepts of Value and 7 Waste come into play.
7 Waste is a concept used to describe the inefficiencies and waste observed in the processes of businesses. These wastes refer to the elements that reduce the efficiency of processes and waste resources. 7 Waste consists of:
-
Overproduction
Producing more than customer demand leads to excess inventory and waste of resources.
-
Wait
Waiting times between processes or at workstations cause inefficiencies and waste of time.
-
Transport
Unnecessary transportation of materials or products leads to waste of time and energy.
-
Process
Unnecessary steps, checkpoints or repetitions increase the complexity of the processes and cause waste of time.
-
Stock
Holding excess inventory increases costs, takes up storage space, and can be a costly way to hide errors.
-
Movement
Unnecessary movements or ergonomic problems at workstations cause inefficiencies and employee fatigue.
-
Errors
Faulty production or faulty operations lead to loss of time and resources and reduce quality.
What We Do
As KPI ACADEMY, we apply different methods to increase efficiency, reduce waste and ensure sustainability in the processes of businesses. With 5S Steps, we adopt the principles of order, cleanliness, standardization, discipline and sustainability in the workplace. With the Lean Factory approach, we optimize business processes and increase efficiency by eliminating waste. By analyzing the concepts of Value and 7 Waste, we identify inefficiencies and waste in business processes and offer improvement opportunities. Our goal is to help businesses achieve operational excellence and gain competitive advantage.
5S Application Examples
Pre
Post


Pre
Post
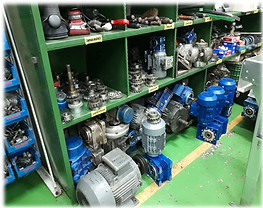
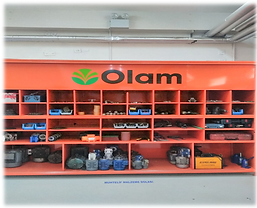
Pre

Post
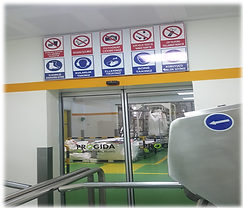
Pre

Post
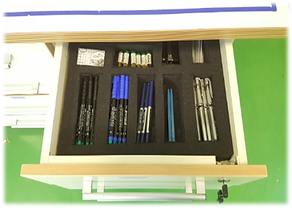